Diante dos problemas econômicos e com um mercado cada vez mais competitivo, as empresas precisam achar soluções para melhorar todo o processo produtivo e se colocar entre as referências da área.
É aí que entra o método lean manufacturing, originário do Japão, após a segunda grande guerra. Esse sistema foi desenvolvido pelo vice-presidente da Toyota na época, Taiichi Ohno. Essa filosofia de gestão visa a combinar técnicas gerenciais e máquinas com o intuito de produzir mais com menos recursos.
A ideia é usar os materiais corretos, no lugar certo, na quantidade ideal, focando na flexibilidade do processo. Também é necessário considerar o uso de um sistema de gestão integrado, para melhorar o controle de todo o processo produtivo e a possibilidade de escalar a produção de maneira facilitada.
Neste texto, vamos apresentar as principais ferramentas de lean manufacturing para avaliar e melhorar a produção da sua empresa. Boa leitura!
1. 5S
O 5S é uma ferramenta baseada em cinco processos simples. Ela vai medir a qualidade da produção e focar na mobilização de toda a companhia de forma lógica.
Criada pelos japoneses, o objetivo é eliminar o desperdício causado por más estações de trabalho e condições. Além disso, o intuito é fazer o monitoramento do que realmente precisa ser produzido, quando produzir e para quem produzir.
Os 5S envolvem os seguintes termos:
- Seiri: evitar o desperdício de recursos e a falta de espaço;
- Seiton: organizar todo o espaço de trabalho para que a produção seja mais efetiva;
- Seiso: trabalhar para que todo o ambiente fique livre e limpo;
- Seiketsu: determinar as normas de triagem, arrumação e limpeza que vão facilitar a ergonomia e a saúde da fábrica;
- Shitsuke: serve para encorajar os seus colaboradores e manter todos ajudando.
2. Jidoka
Essa ferramenta busca automatizar todo o processo de manufatura e é direcionada para o controle de qualidade. A ideia é que um operário cuide de várias máquinas ao mesmo tempo, reduzindo assim o número de pessoas e aumentando a capacidade de produção.
O Jidoka permite que o operador seja capaz de parar todo o processo caso identifique algum erro que aconteceu ou possa acontecer. Dessa forma, toda a fábrica fica ciente do problema e a busca pelo acerto se torna mais efetiva.
3. JIT: Just in time
O Just in Time é uma ferramenta que foca em otimizar a produção. Ou seja, evitar que haja excessos na fabricação que vão deixar o estoque cheio e atrapalhar o desenvolvimento da fábrica.
Se antigamente era comum uma grande quantidade de produtos parados, para substituição dos que saíssem com defeito, hoje em dia, a ideia é trabalhar sempre com o depósito zerado ou mínimo possível.
Assim, a empresa pode obter lucros maiores e conseguir retorno de capital investido mais rápido. Uma vez que vai reduzir os custos com estoque e melhorar a qualidade dos seus produtos.
4. Kanban
Parte essencial do JIT, o Kanban é um sistema que busca a eficiência na fabricação. Por meio de cartões coloridos e de tamanhos diferentes, é possível organizar e direcionar toda a produção para a conclusão das tarefas e demandas.
Ele pode ser feito pelo uso de softwares ou murais. O método separa as tarefas “por fazer”, “em execução” e “concluídas”. Em cada fase, são incluídas ações com uma breve descrição do que precisa ser feito.
Para verificar se o Kanban está sendo eficiente ou não, basta medir o status das tarefas. Se as “por fazer” e “em execução” forem menores que as “já entregues”, isso é um bom sinal. O importante é que o foco seja sempre a otimização do tempo e do processo produtivo.
5. Kaizen
Essa é uma ferramenta focada na qualidade do trabalho. O objetivo é mostrar que todos os funcionários de um determinado local devem se esforçar e trabalhar para reduzir os custos, o desperdício e focar no aumento do lucro.
O Kaizen prega que, para você melhorar a sua produtividade, não precisa fazer grandes investimentos. Basta incentivar os seus colaboradores para que eles se sintam envolvidos com toda a linha de produção.
Ter essa ferramenta implantada na sua empresa vai trazer melhorias na comunicação interna e externa, na autoconfiança de todos os envolvidos e no relacionamento com os seus clientes.
6. PDCA
A melhor forma de verificar se tudo foi executado de acordo com o que foi planejado é pensar no ciclo PDCA. Usado em várias áreas, ele é fácil de aplicar e os resultados aparecem rapidamente.
Essa ferramenta é a abreviação em inglês das etapas para a execução do ciclo. São elas:
- Plan: é o planejamento do seu objetivo final, em que você vai determinar os prazos, as tarefas, os responsáveis etc.;
- Do: a fase “fazer” é o momento em que as atividades são delegadas para cada responsável;
- Check: essa é a fase de acompanhamento, em que temos que verificar se está tudo dentro do prazo, dos custos, da qualidade e de outras variáveis;
- Act: por último, vem o momento de agir ou corrigir, em que vamos verificar se há falhas na execução e no planejamento.
Além de manter todos os colaboradores alinhados com o seu projeto, o ciclo PDCA vai trazer agilidade e qualidade em todas as ações em que ele for implantado.
7. TPM
Total Productive Maintenance ou Manutenção Produtiva Total é uma ferramenta que busca conservar os equipamentos da linha de produção.
Os problemas operacionais podem trazer grandes impactos nas operações manufatureiras. Por isso, essa técnica incentiva a proatividade da manutenção a fim de maximizar os equipamentos operacionais. Combinado com a metodologia 5S, ela apresenta alguns pilares:
- foco na melhoria dos equipamentos;
- manutenção autônoma;
- planos de manutenção;
- gestão de qualidade;
- boa qualidade dos novos equipamentos.
Todos os colaboradores podem pensar em soluções preventivas para evitar quebras, atrasos, defeitos e acidentes com os equipamentos.
8. Heijunka
Essa ferramenta tem como objetivo nivelar a variedade ou o volume da produção. Ela é responsável por dar estabilidade na fabricação e evitar excessos.
9. Andon
A sua função é exclusivamente de gerir os resultados da linha de produção. Tem que ser capaz de detectar e sinalizar problemas em todo o processo industrial.
10. KPIs
Os indicadores-chave de performance são métricas usadas para analisar a eficiência da fábrica. São dados como velocidade de produção e número de produtos entregues que vão conseguir mensurar o sucesso dos objetivos da fabricação.
11. SMED
Sigle Minute Exchange of Die é um conjunto de técnicas que buscam reduzir o tempo que uma máquina demora para ligar. Com isso, a organização consegue ganhar mais tempo e flexibilidade na produção.
Como vimos, o lean manufacturing é um assunto bem complexo e com características bem definidas. No entanto, o mais importante é que, graças às filosofias de gestão dessa técnica, podemos aprimorar e integrar todo o processo de fabricação. É possível reduzir quase a zero os erros e problemas de uma linha de produção.
Você se interessou e quer saber um pouco mais sobre essas ferramentas de lean manufacturing? Assine a nossa newsletter e receba e-mails com os melhores conteúdos, para você aprender mais e aplicar as melhores técnicas no seu negócio!
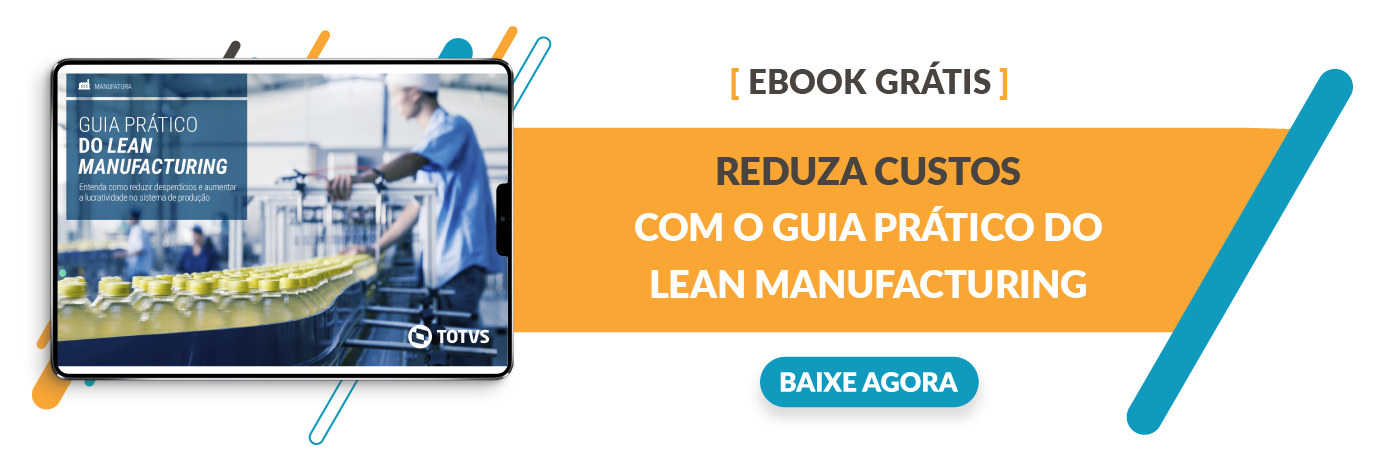
Deixe aqui seu comentário